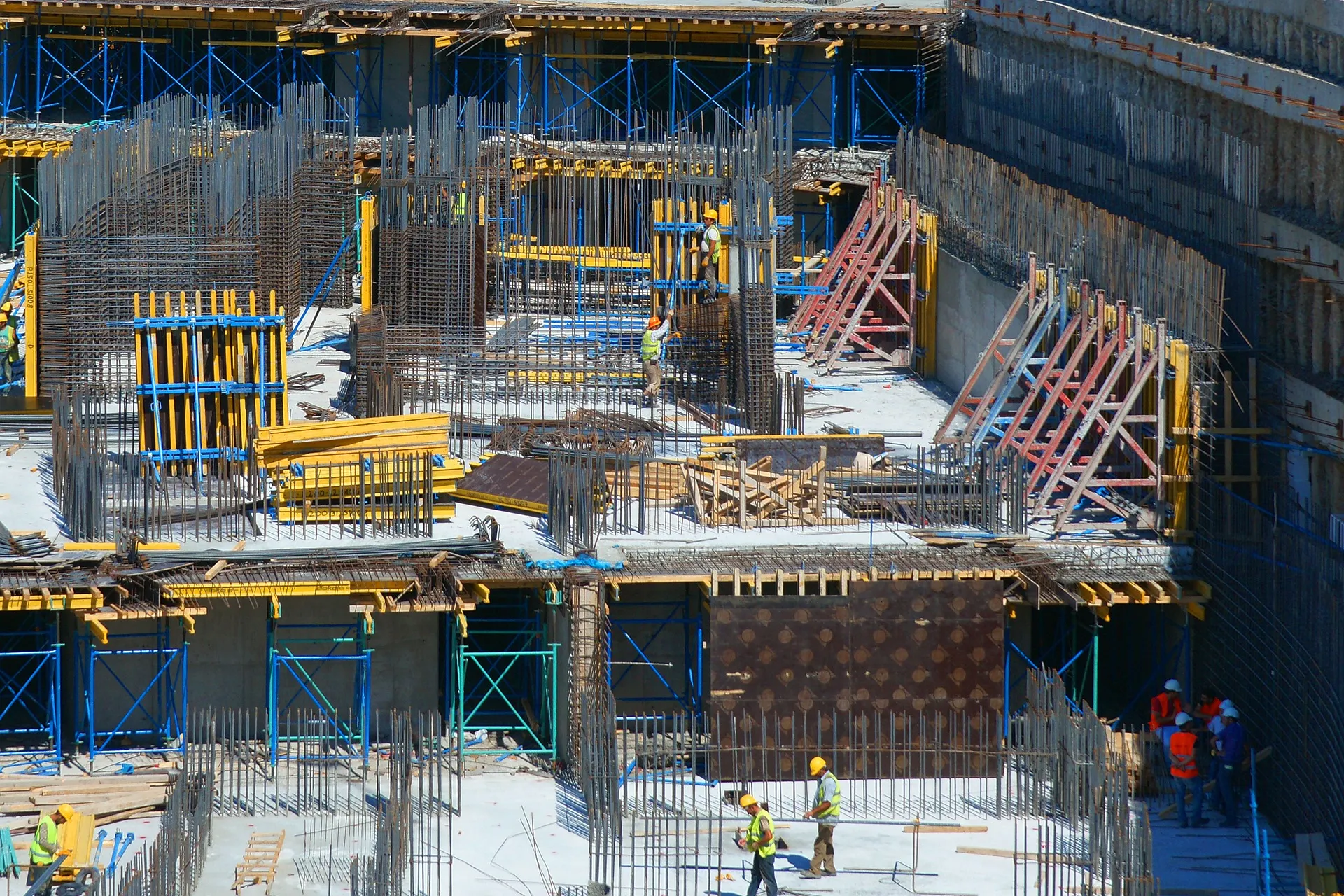
Construction Inventory Management That Works
There are an endless number of inventory management solutions that claim to work for the construction industry. However, inventory management needs in construction are different and specific. Software designed for multiple industries will be loaded with complexity and features that are irrelevant to construction while likely missing critical features that you need.
To begin with, asset types are unique to the industry and should be managed accordingly. The four types of assets in construction are tools, equipment, consumables, and materials.
Tools and equipment move across multiple inventory locations, where usage and cost are often tracked. For more expensive tools and equipment (concrete saws, generators, lifts), the specific item needs to be tracked. However, with less expensive items like hand tools and caution cones, only the number of items matters. Large equipment will most likely need to be recorded as an asset on the books, while the treatment of tools will vary by company.
Consumables include items (saw blades, grinding wheels, welding wire) that are not expected to be returned and are often taken off the books as soon as they are transferred to a construction project. Materials (pipe, conduit, steel studs) require close management with suppliers and are often only stored on the project site.
Multiple inventory locations in construction can include warehouses, laydown yards, job sites, employee trucks, or the office. Construction Inventory Management software solutions must allow easy transfer of assets across the various locations while providing visibility to where the assets are in near real-time. For example, suppose you need four rotary hammers for a project. In that case, you need visibility to how many are in the warehouse and not currently being used on other projects and the ability to request them to be transferred.
Seamless check-in/out processes are essential for employee accountability without slowing the employees down with complex workflows. In the example above, it's not only critical to understand what rotary hammers are available and get them transferred but also that the employees confirm they have received them on the construction site. Otherwise, inventory counts across the various locations will quickly become inaccurate, and your system will break down.
In addition to the different asset types and inventory locations, consider the following points when selecting an inventory management system for construction:
-
Manual processes are common but inadequate.
Most subcontractors and self-performing GCs have over 1000 assets across the different asset types and locations outlined above. Combined with all the almost daily project changes, it's nearly impossible to manage inventory levels manually and accurately. These inefficiencies can cost significant time and money in an industry where profit margins are already tight.
-
Replace manual processes with simple software.
By nature, many in the industry still use manual processes. Users migrating from a manual process will not likely adopt complex software or workflows. Ideally, your inventory system should work with your existing workflows by automating the manual steps to save time and improve accuracy.
-
Opt for transparency and visibility.
When everyone can see who is responsible for what assets, then accountability is also clear and understood. This helps ensure that employees are not purchasing tools and materials that you already have in the shop or on a nearby job site. Look for cloud-based solutions that update in real-time. This keeps inventory accurate so items can be found when needed.
-
Improved accountability reduces job site theft.
If your employees are taking responsibility for the tools, then they are more likely to keep a closer eye on them. This also helps with misplaced tools, which are far more common than stolen tools.
You will find a wide range of software capabilities and prices when evaluating inventory management software designed specifically for construction. We recommend determining your priorities and looking for software that focuses on what is vital to your construction company. Instead, many IT managers choose the product with the most features. Excessive features and options add complexity to software and can confuse new or “non-technical” users who need to use the software.
There are complex solutions designed for large organizations that include features like vendor order management, creating purchase orders and accounting integrations. The pricing and complexity will likely not make sense if you have less than 500 employees.
TOOLTRIBE is an example of a tool-tracking app that works for tool inventory, equipment, consumables, and other bulk (quantity items). The cloud-based tool tracking system allows items to be transferred and tracked across multiple locations while providing real-time visibility and transparency to all inventory.
Inventory management is crucial to maximizing your profit in construction. Finding the right software solution will drive if and how your employees will embrace the new process. We highly recommend finding a solution focused on the construction industry and your specific business needs. Please contact us with any questions or to learn more about how TOOLTRIBE can help your business.